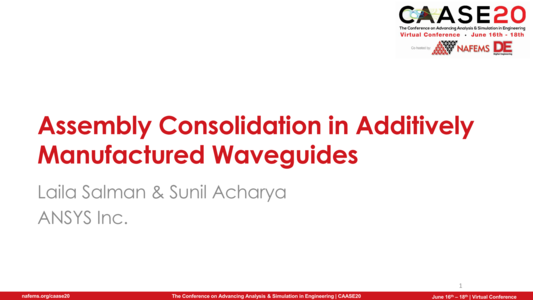
NAFEMS Americas and Digital Engineering (DE) teamed up (once again) to present CAASE, the (now Virtual) Conference on Advancing Analysis & Simulation in Engineering, on June 16-18, 2020!
CAASE20 brought together the leading visionaries, developers, and practitioners of CAE-related technologies in an open forum, unlike any other, to share experiences, discuss relevant trends, discover common themes, and explore future issues, including:
-What is the future for engineering analysis and simulation?
-Where will it lead us in the next decade?
-How can designers and engineers realize its full potential?
What are the business, technological, and human enablers that will take past successful developments to new levels in the next ten years?
Resource AbstractRecently, powder-bed fusion metal Additive Manufacturing (AM) process has matured as a breakthrough technology for the development of RF and microwave components such as waveguides, filters as well as antennas. This enabling technology has the potential and flexibility to build any shape components that conventional machining can rather be complex or not possible to use. Additive Manufacturing or 3D Printing will play key role in the future of microwave and millimeter wave applications’ manufacturing processes. It will allow the exploration of unique and optimized designs of parts as well as assembly consolidation. Today, AM is highly anticipated as a standard manufacturing technology that can be widely utilized in large number of industrial applications including medical implants and disposable surgical instruments to aerospace forming equipment. As a result, AM has gained popularity offering engineers and designers the capability of building customized and optimized designs with enhanced RF, thermal and mechanical performance.
The presented work illustrates the use of multi-physics simulation techniques in the design and optimization of an RF waveguide assembly that integrates three RF functionalities including bending, twisting and filtering sections operating in Ku/K-Band. The monolithic WR51 component was additively manufactured [1]. The consolidated, multi RF-functional, mechanical part was measured with respect to individual conventional waveguide components. Measurements assured the unique features that AM can offer with 3-D metal printing in the miniaturization and integration of waveguide systems as well as material mass reduction which certainly justifies the adoption of this technology in building RF space components and satellite communication systems.
The demonstrated workflow can be generalized to wide variety of radio frequency applications such as phased array antennas with complex feeding networks or multi-beam active antenna array with polarizers, filters, couplers and power dividers. Moreover, the same workflow can significantly accelerate the development process of high throughput satellite communication systems with multibeam architecture and large feed chains while reducing the form-factor and the losses at the same time. The process simulation methodologies for the selective laser sintering presented in this work allows for reduced waste and build time while maintaining adequate support structure during the manufacturing of the component. Additionally, coupling with thermal-structural FEA simulation capabilities can be done to capture relative thermal losses and their effect on the high frequency performance. While the monolithic component offers significantly small form factor, flexibility of AM allows further weight reduction through topology optimization techniques. This is important in satellite communications technology where any reduction in payload weight is considered advantageous.
Several optimized design approaches are shown with relevant merits. The combined twisting, filtering and bending functions in the single component creates internal surfaces at varying angles to the build direction. Internal support requirements can generate additional postprocessing challenges. This is where CAE based support generation tools can be well utilized to find the optimum build time while minimizing the distortion tendencies and the support volume. Once the optimum supports and build orientations are obtained, a coupled thermal-structural FEA simulation can be used to simulate the AM build process and estimate the residual stresses in the build for a specific build orientation and support strategy.
[1] Pevereni O A, Lumia M, Paonessa F, Virone G, Calignano F, Cattano G, Manfredi D, IEEE TRANSACTIONS ON MICROWAVE THEORY AND TECHNIQUES, VOL. 66, NO. 5, MAY 2018.