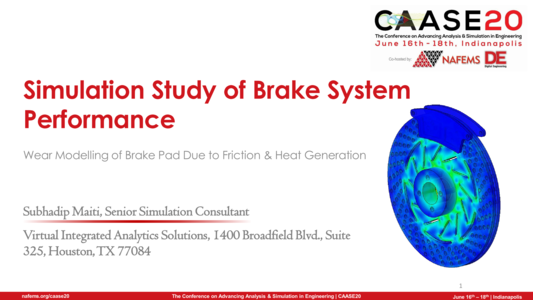
NAFEMS Americas and Digital Engineering (DE) teamed up (once again) to present CAASE, the (now Virtual) Conference on Advancing Analysis & Simulation in Engineering, on June 16-18, 2020!
CAASE20 brought together the leading visionaries, developers, and practitioners of CAE-related technologies in an open forum, unlike any other, to share experiences, discuss relevant trends, discover common themes, and explore future issues, including:
-What is the future for engineering analysis and simulation?
-Where will it lead us in the next decade?
-How can designers and engineers realize its full potential?
What are the business, technological, and human enablers that will take past successful developments to new levels in the next ten years?
Resource AbstractThe vehicle brake system plays an important role in the safety of the occupant during the on-road driving scenario. However the braking performance gets degraded over time due the frictional heat generation which ultimately effects in numerous ways like wear and tear, thermal cracks, noise and vibration issues, etc. The friction and the relative motion between the contacting parts generate heat due to frictional sliding. Some of the heat gets dissipated in the environment, but if the rate of heat generation is higher than the dissipated energy, temperature starts to rise at the adjacent components. Large friction coefficients, Rapid changes in contact pressure, Strong material dependence on temperature, Significant plastic dissipation makes this class problem to be numerically expensive to solve. In this presentation, the brake pad reliability and the thermal behavior of the multiple small scale components of the brake rotor system are investigated using the fully coupled temperature-displacement analysis using general-purpose FEA solution ABAQUS. Further, the effect of rotor speed and friction coefficient on the thermal performance of the brake pad is been evaluated.
Also, the continuous/intermittent operations of the braking system lead the brake pad to have wear and deteriorating performance in long run. The progressive damage caused by the relative motion of two contacting surfaces generates a loss of material or produce a change in geometry if allowed to progress without limit. The wear rate is assumed to be a function of hardness of the material, contact pressure and slip velocity between the contacting parts. Using the “adaptive meshing” technology in Abaqus/Standard, along with user subroutine UMESHMOTION, allows incorporation of general wear laws helps to predict wear behavior accurately. In this presentation, the results obtained from the finite element analysis and how the output solution relates to the phenomena of the wear/damage to the practical situation is been discussed.