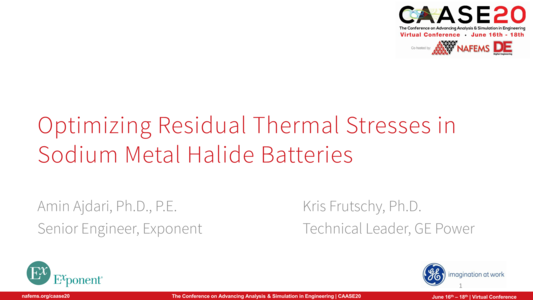
NAFEMS Americas and Digital Engineering (DE) teamed up (once again) to present CAASE, the (now Virtual) Conference on Advancing Analysis & Simulation in Engineering, on June 16-18, 2020!
CAASE20 brought together the leading visionaries, developers, and practitioners of CAE-related technologies in an open forum, unlike any other, to share experiences, discuss relevant trends, discover common themes, and explore future issues, including:
-What is the future for engineering analysis and simulation?
-Where will it lead us in the next decade?
-How can designers and engineers realize its full potential?
What are the business, technological, and human enablers that will take past successful developments to new levels in the next ten years?
Resource AbstractHigh temperature batteries such as sodium-metal-halide and sodium-sulphur batteries experience extreme thermal conditions during manufacturing and operation. Temperature changes develop residual thermal stresses, where there is a difference in the coefficient of thermal expansion (CTE) between neighboring components. Residual stresses and total strain energy of deformed components could potentially result in crack initiation and subsequently crack propagation. In this work, residual thermal stresses in the glass seal area of a generic cell undergoing thermal shock are evaluated using Finite Element Analysis (FEA).
To optimize the residual thermal stresses, this work focuses on the thermal characteristics of the glass seal material such as the set temperature and CTE value. Thermo-mechanical FEA analysis was used to quantify the max principal stresses in the glass seal and the ceramic tube. Total strain energy in the glass seal area (consisting of glass seal, ceramic tube and the collar) was also looked at as the other two variables.
Variation in total strain energies and residual stresses are quantified for a range of thermal material properties and the resultant response surface is used to identify example glass materials which could minimize the max principal stresses and total strain energy in the glass seal area. Four example glasses are examined to optimize all three variables: max principal stress in the glass seal, max principal stress in the ceramic tube, and total strain energy in the glass seal area.
Results indicate a glass seal with higher CTE and higher set temperature, in general, will increase the principal stress in the glass seal as well as the ceramic tube when the entire cell undergoes a thermal cooling. Total strain energy in the glass seal area, however, has a minimum quantity depending on the CTE value and the set temperature.