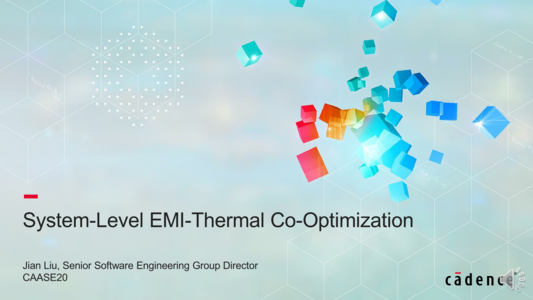
NAFEMS Americas and Digital Engineering (DE) teamed up (once again) to present CAASE, the (now Virtual) Conference on Advancing Analysis & Simulation in Engineering, on June 16-18, 2020!
CAASE20 brought together the leading visionaries, developers, and practitioners of CAE-related technologies in an open forum, unlike any other, to share experiences, discuss relevant trends, discover common themes, and explore future issues, including:
-What is the future for engineering analysis and simulation?
-Where will it lead us in the next decade?
-How can designers and engineers realize its full potential?
What are the business, technological, and human enablers that will take past successful developments to new levels in the next ten years?
Resource AbstractWith the fast development and deployment of autonomous cars, the design of electronic components is becoming more challenging due to increased power consumption, strong electromagnetic radiation and interference, and demanding thermal dissipation. The traditional bottom up design flow, which starts from IC to PCB, and then from PCB to the metal enclosure box, may not be sufficient if any EMI and thermal violations are found in the late design stages. Any detected failure means a design re-spin, a longer design cycle, increased NRE and possible higher product cost that may render the product non-competitive
This paper proposes a system level EMI-thermal co-simulation and optimization method. It will provide guidance in system-level design through simulation with a digital twin. With the given physical model, an EMI model and a thermal model will be created and simulated efficiently. More specifically, the high power components on the PCB, which contribute the most to both the EMI and thermal, are placed in various locations to create the contour graphs for both electromagnetic radiation and temperature distribution. The overlap of these graphs will give the optimized location which satisfy both EMI and thermal constraints. Solid and fluid system level thermal analysis enables component level accuracy to create detailed thermal contour models efficiently. Massive parallel computation engines are used to support speed and capacity. As for the electromagnetic analysis, a 3D FDTD solver is employed. Again, massive parallel computation engines are employed to solve for large physical spaces in a short time period. The distributed computation architecture enables the analysis of much larger and complicated structures which are difficult for non-structured mesh based EM solvers. We will demonstrate how using the same mechanical CAD GUI interface, enables multiple physics analysis and optimization to take place on a single desktop in a single canvas. We will then discuss future projects where more physical constraints may be incorporated into the pre-design optimization process.