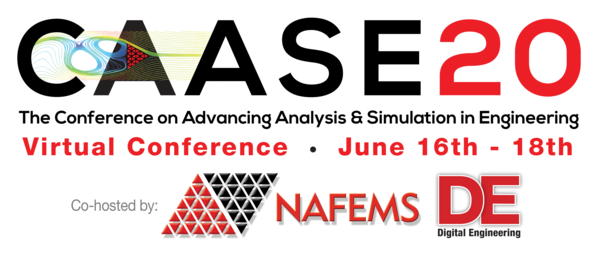
NAFEMS Americas and Digital Engineering (DE) teamed up (once again) to present CAASE, the (now Virtual) Conference on Advancing Analysis & Simulation in Engineering, on June 16-18, 2020!
CAASE20 brought together the leading visionaries, developers, and practitioners of CAE-related technologies in an open forum, unlike any other, to share experiences, discuss relevant trends, discover common themes, and explore future issues, including:
-What is the future for engineering analysis and simulation?
-Where will it lead us in the next decade?
-How can designers and engineers realize its full potential?
What are the business, technological, and human enablers that will take past successful developments to new levels in the next ten years?
Resource AbstractWhen operating on the ground transportation vehicles, rotary equipment such as cooling fan blades are subject to a variety of loads including aerodynamic pressures, harmonic or random vibrations and centrifugal effects. In addition, because of the rotational nature of their function, the fans may show various undesirable behaviors that could be induced or magnified by the external loads. Most important of such unwanted response is resonance condition that occurs at critical speeds. High levels of structural strain and stress are observed under resonance conditions. To ensure durability and robustness of the cooling fans, several physical tests must be carried out during the design process to achieve final design verification. Of course, these tests have their own limitations, for example, monitoring all physical locations on the components is impossible. We present here how CAE simulation (Finite element and CFD analyses) can eliminate the need of such expensive and lengthy physical tests by capturing critical speeds and predicting stress levels at such conditions on the whole component. This is accomplished by obtaining Campbell Diagram for the fan component, identifying critical speeds that has been proven to be in close correlation with test data. We also show how dynamic analysis models transient and steady-state response of the rotating fan at those rotational speeds by introducing harmonic and non-symmetric aerodynamic pressure profiles as well as centrifugal effects. Total stress levels simulated by our method are in a very good correlation with existing test data. The frequency content of the input and output variables in the CAE model are consistent with what is observed in the actual experimental data. It is demonstrated that centrifugal effects are the major contributor to the stress levels except on the resonance conditions where the aerodynamic loads play major effect. Our method will allow faster and more efficient design process.