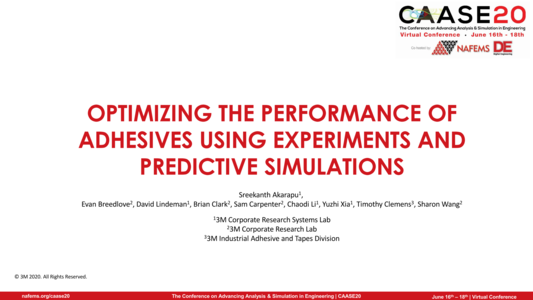
NAFEMS Americas and Digital Engineering (DE) teamed up (once again) to present CAASE, the (now Virtual) Conference on Advancing Analysis & Simulation in Engineering, on June 16-18, 2020!
CAASE20 brought together the leading visionaries, developers, and practitioners of CAE-related technologies in an open forum, unlike any other, to share experiences, discuss relevant trends, discover common themes, and explore future issues, including:
-What is the future for engineering analysis and simulation?
-Where will it lead us in the next decade?
-How can designers and engineers realize its full potential?
What are the business, technological, and human enablers that will take past successful developments to new levels in the next ten years?
Resource AbstractAdhesives (pressure sensitive and structural) can be designed to have structural load bearing capacity and can have many advantages over traditional joining technologies such as bolting, brazing and welding. From an energy and environmental aspect, adhesives enable light-weight aerospace and automotive components with a significant impact on improving fuel efficiency and reducing harmful environmental impact. Accurate structural analysis of adhesive-containing structures requires reliable material descriptions for bonds; however, many adhesives are soft materials which undergo large deformation and exhibit rate-dependent behavior. Therefore, understanding the adhesive behavior in a wide range of strain rates and operating temperatures is key to assess as well as predict product reliability. Towards this goal, 3M has developed novel experimental methods and advanced material models which accurately capture both large deformation and rate-dependent behavior. These material models are suitable for static and dynamic analysis, including impact.
In the age of Industry 4.0, 3M is spearheading and setting a trend of digital material cards (DMC) to help various industries realize their digitization vision. In this talk, we discuss our methodology of careful calibration and validation of 3M material models and state of the art digitization of these models into DMCs in various formats amenable to commercially available general purpose finite element software packages. We also discuss and showcase the usage of these material models in a scooter assembled using only adhesive tapes. This case study will focus on workflow of a predictive simulation using 3M DMC which is capable of modeling material behavior in various service conditions. Comparisons to traditional material modeling strategies will be given. We will further demonstrate the necessity of modeling structural adhesives and pressure-sensitive adhesives using different material modeling paradigms, including an analysis of predictive errors observed when cohesive zone models are applied to structural adhesives. A brief overview of 3M communication portals to learn more about our adhesives and means to try DMC will also be presented.