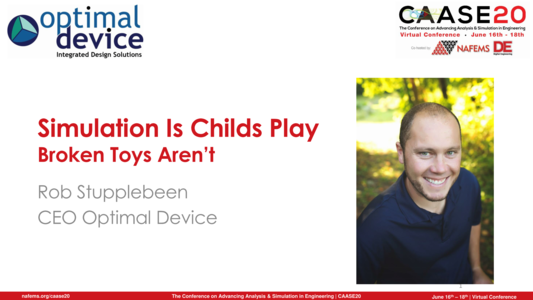
NAFEMS Americas and Digital Engineering (DE) teamed up (once again) to present CAASE, the (now Virtual) Conference on Advancing Analysis & Simulation in Engineering, on June 16-18, 2020!
CAASE20 brought together the leading visionaries, developers, and practitioners of CAE-related technologies in an open forum, unlike any other, to share experiences, discuss relevant trends, discover common themes, and explore future issues, including:
-What is the future for engineering analysis and simulation?
-Where will it lead us in the next decade?
-How can designers and engineers realize its full potential?
What are the business, technological, and human enablers that will take past successful developments to new levels in the next ten years?
Resource AbstractThis is a case study of multiple knit line failures on the popular fidget spinner toy. This toy’s geometry has been reverse engineered to create suitable geometry for a variety of simulations and redesigns. From an injection molding standpoint, the three lobed design, with 4 holes allow for a deceptively difficult molding problem. Knit lines are inevitable but where should the gates be located and where will the knit likes be located? Injection molding simulation is used to investigate a variety of gate locations and the use of multiple gates. Once the molding technique has been selected what can be done to maximize the strength of the part without deviating too far from the iconic design? Finite element analysis is performed to simulate the stresses induced through press fitting of the bearings. The simulation was carried out by having the bearings in place using contact with removing overclosures. This method is more computationally efficient than pressing the bearing in which would include sliding contact. The bearing insertion causes hoop stresses in each lobe. These stresses put the knit lines in tension which causes part failure. We will assume that the locations and sizes of the bearings are fixed and the outside diameter for ergonomic reasons. This sets the allowable design space for the redesign. Shape optimization was then used to evolve the design to maximize strength and stiffness while minimizing weight and cost. The locations of the knit lines were assigned material properties of reduced strength. Redesigning the geometry will modify the mold flow and the knit line locations causing an iterative feedback loop which can be handled with either a coupled or sequential workflow.
In this study multiple simulation tools were used to reverse engineer the root causes for the product failure. These failures could have been predicted and designed around allowing for a more robust product and avoiding product failures. Most importantly broken toys could be avoided!
us