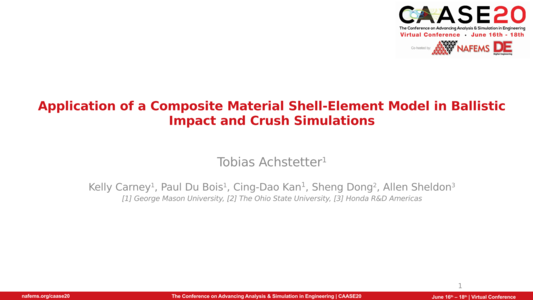
NAFEMS Americas and Digital Engineering (DE) teamed up (once again) to present CAASE, the (now Virtual) Conference on Advancing Analysis & Simulation in Engineering, on June 16-18, 2020!
CAASE20 brought together the leading visionaries, developers, and practitioners of CAE-related technologies in an open forum, unlike any other, to share experiences, discuss relevant trends, discover common themes, and explore future issues, including:
-What is the future for engineering analysis and simulation?
-Where will it lead us in the next decade?
-How can designers and engineers realize its full potential?
What are the business, technological, and human enablers that will take past successful developments to new levels in the next ten years?
Resource AbstractWhile the response to loading of traditional engineering materials, such as plastics and steel, is well understood and can be simulated accurately, designers of composite structures still rely heavily on physical testing of components to ensure the requirements of load bearing capabilities are met.
The majority of composite material models that have been developed rely on non-physical material parameters that have to be calibrated in extensive simulations. A predictive model, based on physically meaningful input, is currently not available.
The developed orthotropic material model includes the ability to define tabulated hardening curves for different loading directions with strain-rate and temperature dependency. Strain-rate dependency was achieved by coupling the theories of viscoelasticity and viscoplasticity to allow for rate dependency in both the elastic and plastic regions of the material deformation. A damage model was implemented, where a reduction of stiffness and stress degradation in the individual material directions can be tracked precisely. Modeling of failure and Finite Element erosion was achieved by implementing a new strain-based generalized tabulated failure criterion, where failure strains can be precisely defined for specific states of stresses.
The material model was implemented into the commercial finite element software LS-DYNA and was utilized to simulate ballistic impacts and a C-channel under crush loading. These validation simulations of the material model were performed to test the physical usefulness and robustness of the developed material model.
Ballistic impact tests were chosen to highlight the capabilities of the material model in high speed impact applications. For the tested unidirectional composite material in the ballistic impact, extensive material data was available.
In a recent study, Dong et al. calibrated an existing material model in crush simulations to match force-displacement characteristics of several crush experiments and a match between tests and simulations was achieved after several rounds of optimization. To highlight the capabilities of the new material model in crush load cases, its results were compared to the force-time history obtained in tests and simulations using MAT58.
For both the ballistic impact and crush simulations, the same modeling approach was used.