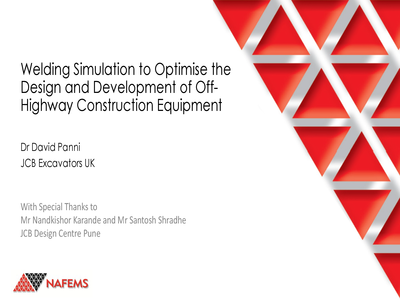
This presentation was made at the NAFEMS UK Seminar "Welding Simlation - How Much Validation is Enough?"
Resource AbstractThe use of arc-welded steel fabrications has proven itself durable in the off-highway vehicle industry over many years and there is considerable qualitative experience in selecting the correct welding parameters. However, the process of designing fixtures, optimising welding parameters and validating them is a highly time-consuming, iterative and expensive process. Often the results are sub-optimal.
More recently, simulation tools have become available to help Design and Manufacturing Engineers optimise their designs at an early stage in the process to reduce cost and time to market.
This paper/presentation outlines the historic process for proving out fabrications and then gives various case studies where up-front weld simulations have been successfully used to optimise weld parameters, reduce distortion and improve weld penetration while reducing the amount of physical testing required.
The paper is presented specifically from the perspective of an end-user and how the technologies fit into a very pragmatic product development process. It specifically aims to give an insight into the question of ‘how much validation is enough’ from an industrial perspective.
Many of the case studies presented here have been done by colleagues in India.
The presentation is vendor agnostic. Various alternative tools are available for weld modelling but the case studies here have been performed using SysweldTM by ESI.
Typical joining processes in the Off-highway industry are manual or robot MIG/MAG welding of carbon-steel plates with thicknesses in the range of 8-12mm for primary load-bearing structures. Some thin walled structures, typically 2-3mm can also be found on cabs and cab door welded assemblies. This presentation covers examples of both thick and thin wall welded assemblies.
The presentation describes the traditional ‘trial and error’ approach to optimising welding procedures to minimise distortion. It then describes how a simulation driven approach can significantly reduce lead times by between 25% and 35%, reduce the number of physical trials by up to 60% and reduce the development costs accordingly.
The presentation then describes the steps taken to create a model and the input parameters.
The key question of how accurate is good enough is addressed through the case studies. In our experience we have seen that the goal does not need to be 100% or even 90% accuracy. In most cases accuracies of 70% are acceptable. The results invariably capture the overall behaviour of the welded assembly correctly; thus giving the Design and Welding Engineers an insight into which parameters have the greatest effect on distortion and which ones to change.
At present the work has focussed on weld distortion. However, future developments may look into residual stresses. The effect of these on fatigue life are well known but they are difficult and expensive to measure. A better understanding of these through simulation may give a deeper insight into the durability of off-highway products which are subjected to extreme loading conditions.
Despite being faster than the traditional ‘trial and error’ approach bottlenecks in the simulation process are identified and these are discussed.