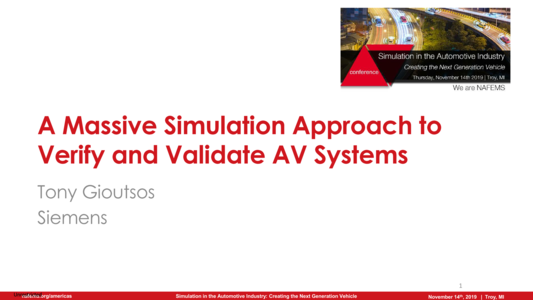
This presentation was made at the NAFEMS Americas "Creating the Next Generation Vehicle" held on the 14th of November in Troy.
The automotive engineering community is now confronting the largest technology transformation since its inception. This includes the electrification of powertrains for more efficient consumption and cleaner emissions, the reinvention of the battery with fast wireless charging capabilities and finally the advent of a fully autonomous vehicle. Compounding to these technology changes, the automotive companies design verification process is moving away from a major reliance on physical testing to almost a full virtual simulation product verification process.
The automotive engineering community is now confronting the largest technology transformation since its inception. This includes the electrification of powertrains for more efficient consumption and cleaner emissions, the reinvention of the battery with fast wireless charging capabilities and finally the advent of a fully autonomous vehicle. Compounding to these technology changes, the automotive companies design verification process is moving away from a major reliance on physical testing to almost a full virtual simulation product verification process.
Resource AbstractVerification and Validation (V & V) of Highly Automated Vehicles (HAV) requires the use of massive simulation. With massive simulation we can create a DOE and Monte Carlo series of tests. These test results can be correlated to desired results by using standard Estimation and Detection principles. For example, for a detection case (e.g. Automatic Emergency Braking (AEB)), a Receiver Operating Characteristic (ROC) curve can be computed. The ROC curve creates a V & V of the AEB system.
To start this process, we must begin with appropriate scenarios. Scenarios are very important in establishing the “base” set of tests that our system must be concerned with. These “edge” cases could come from various sources including: Euro NCAP, Data Collection, GIDAS, CIDAS, AMP, KITI, Streetwise, Open Scenario, Open CRG, MCity ABC, ASAM, etc. Once the base set is defined, we can move on to sensor modelling.
The next step in the process involves correct sensor modelling as well as associated perception and control algorithms. With accurate sensor models, simulation via SIL, HIL, DIL or VIL can vastly reduce the need for test track testing and field testing. By linking the complex world to Physics based sensor models, this goal can be reached. We next turn our attention to the sensor models themselves and in particular, we focus on the detailed physics models for camera, RADAR, LIDAR and V2X.
Below is an example of a Detailed Physics Based Radar model. The left side of the image is the camera view of a vehicle as it drives through a scene. The right side is what is commonly called a “range-doppler” image of the same scene. The range-doppler image is a somewhat processed version of the raw radar data. It depicts radar cross section versus the range and relative velocity to our ego vehicle. This has been correlated to real data by working with various sensor manufacturers and suppliers.
Once the sensor models are chosen, deterministic and stochastic variations can be used to widely vary the scenario database. This will create massive variations that help produce the V & V framework for analysis. Some examples of the variation could include: sensor noise, actor trajectories, weather and/or lighting variation, road variation, lane line variation (fading and holes), traffic sign degradation, variations of traffic, actor variations, vehicle motion stochastic variation, sensor mounting variation (dynamic and static), etc.
There should be orchestration of the variations and a complete tracking to allow for “playback” of situations that do not meet expectations. and computing on a cloud or cluster solution. Analysing the results and correlating them to a set of requirements can lead to a proper V&V of the entire HAV system.
In addition to the generic HAV system (i.e. world and sensor models), digital twins of the vehicle, occupant and tires should also be added to the process. The tires are the only part of the vehicle touching the ground and play an important part of the overall analysis. Finally, the occupant(s) in the vehicle is(are) what matter most. It should be apparent that safety will be the critical issue, so that when the HAV system does not meet expectations, analysis of the impact on the occupant(s) can be performed.