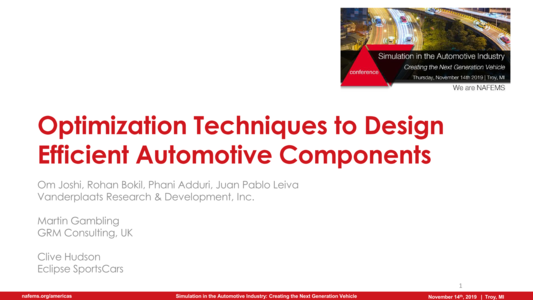
This presentation was made at the NAFEMS Americas "Creating the Next Generation Vehicle" held on the 14th of November in Troy.
The automotive engineering community is now confronting the largest technology transformation since its inception. This includes the electrification of powertrains for more efficient consumption and cleaner emissions, the reinvention of the battery with fast wireless charging capabilities and finally the advent of a fully autonomous vehicle. Compounding to these technology changes, the automotive companies design verification process is moving away from a major reliance on physical testing to almost a full virtual simulation product verification process.
The automotive engineering community is now confronting the largest technology transformation since its inception. This includes the electrification of powertrains for more efficient consumption and cleaner emissions, the reinvention of the battery with fast wireless charging capabilities and finally the advent of a fully autonomous vehicle. Compounding to these technology changes, the automotive companies design verification process is moving away from a major reliance on physical testing to almost a full virtual simulation product verification process.
Resource AbstractIn today’s competitive and ever-demanding business environment, designers and engineers are in a constant search for ways to design better and more efficient products with minimum resource utilization. This presentation will discuss two optimization techniques developed to address these needs. The first optimization technique uses design of experiments and response surface approximation. The second optimization technique uses direct optimization method with no approximations. These two optimization techniques will be illustrated with corresponding two case studies from the automotive industry.
In the first case study, the optimal design of a diffuser from Eclipse Sports Car is presented. In this study four CAD parameters, which defined the shape of the diffuser geometry, were used as design variables. The car drag was minimized and the downforce value was maximized. The Latin Hypercube design of experiment (DOE) design was used to generate initial set of design points and build a response surface approximation for the drag and the downforce. The Response surface approximation-based optimization technique was used to find the optimum configuration for the diffuser geometry. The optimum diffuser design was then validated by conducting aerodynamic tests of the car with the manufactured diffuser.
The second case study is sizing optimization of a body-in-white structure to minimize the mass while maintaining the several performance target on corresponding load cases. In this study 30 design variables were used to design thicknesses of main parts of the car body. A finite element analysis of the structure was conducted for seven different load cases. The optimization algorithms were coupled with a finite element analysis code to perform the optimization study. After optimization, post-processing methods were used for performing design space exploration and for further design improvements.
The optimization techniques used in the above two case studies allows designers and engineers to get valuable insights on the performance of their designs and to ultimately produce efficient automotive components.