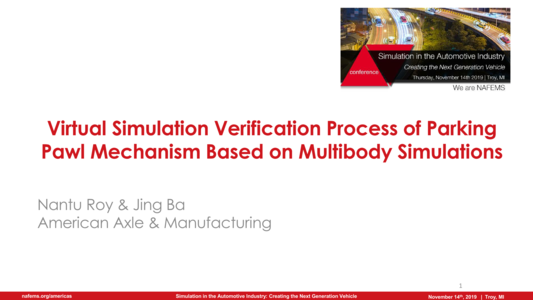
This presentation was made at the NAFEMS Americas "Creating the Next Generation Vehicle" held on the 14th of November in Troy.
The automotive engineering community is now confronting the largest technology transformation since its inception. This includes the electrification of powertrains for more efficient consumption and cleaner emissions, the reinvention of the battery with fast wireless charging capabilities and finally the advent of a fully autonomous vehicle. Compounding to these technology changes, the automotive companies design verification process is moving away from a major reliance on physical testing to almost a full virtual simulation product verification process.
The automotive engineering community is now confronting the largest technology transformation since its inception. This includes the electrification of powertrains for more efficient consumption and cleaner emissions, the reinvention of the battery with fast wireless charging capabilities and finally the advent of a fully autonomous vehicle. Compounding to these technology changes, the automotive companies design verification process is moving away from a major reliance on physical testing to almost a full virtual simulation product verification process.
Resource AbstractGlobalisation coupled with reduced and better prototypes, and shorter product development time and reduced cost have spearheaded new levels of competition among automotive manufacturers. The standard design verification process in practice is moving away from a major reliance on physical testing to almost a full virtual simulation product verification process allowing virtual build and validation processes occur concurrently. However, this poses enormous challenges to the CAE engineers as they require a significant increase in the upfront use of numerical simulation capabilities, methods and processes.
A vehicle with automatic transmission is fitted with a parking pawl mechanism to avoid the risk posed by unintended vehicle movement. The system has to be robust enough to function safely even in poor tolerance situations, under extreme temperatures and rigorous durability tests. Thorough study is required in the design and approval of a parking mechanism. In this presentation, virtual validation of parking pawl mechanism focusing on early detection and isolation of design flaws, predicting, and optimizing the dynamic characteristics is discussed. A detailed dynamic model was developed in ADAMS with proper solver settings, elastic body, damping and contact formulations.
Virtual build should replicate a product’s physical behaviour to provide confidence, among engineers and designers, in the virtual tests. A method to integrate virtual and physical testing is proposed in this work. Tolerance setting of parking pawl mechanism parts and assemblies is assessed as its function is to balance the system functionality with economic factors. Excessively tight tolerances will add cost due to more complex processing stages whereas inadequately wide tolerances will result in insufficient quality and costly rework. Virtual prototypes were built and tested in ADAMS to observe component interactions, and identify the underlying factors. The virtual test rig was also used to capture dynamic load and motion signals at various interfaces, and served as inputs to component FEA for structural evaluations.