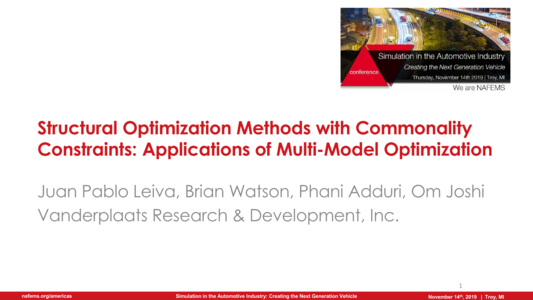
This presentation was made at the NAFEMS Americas "Creating the Next Generation Vehicle" held on the 14th of November in Troy.
The automotive engineering community is now confronting the largest technology transformation since its inception. This includes the electrification of powertrains for more efficient consumption and cleaner emissions, the reinvention of the battery with fast wireless charging capabilities and finally the advent of a fully autonomous vehicle. Compounding to these technology changes, the automotive companies design verification process is moving away from a major reliance on physical testing to almost a full virtual simulation product verification process.
The automotive engineering community is now confronting the largest technology transformation since its inception. This includes the electrification of powertrains for more efficient consumption and cleaner emissions, the reinvention of the battery with fast wireless charging capabilities and finally the advent of a fully autonomous vehicle. Compounding to these technology changes, the automotive companies design verification process is moving away from a major reliance on physical testing to almost a full virtual simulation product verification process.
Resource AbstractIn today’s competitive markets, companies are constantly looking for ways to reduce cost. Optimization techniques are now frequently used as they can be directly applied to reduce mass or cost while meeting or exceeding performance targets. Standardization has brought lower prices as standard parts can be mass produced and/or purchased in bulk. In this paper, we discuss combining both ideas: optimize individual components and simultaneously optimize for shared components among multiple similar products. To achieve optimal component commonality we use multi-model optimization (MMO). MMO allows multiple optimization models to run simultaneously via a master optimization process. The individual sub-models may share some or all of their design variables with other sub-models. Each sub-model may include its own private constraints and objectives. Using multi-model optimization, large-scale optimization problems may be solved on HPC clusters, with each sub model analysis solver running on a separate compute node. The key benefits of multi-model optimization are: a) the ability to optimize large-scale models where designable regions are common to several model assemblies, but remaining parts of the models differ. For example, optimization of components common to several configurations of a vehicle, such as sedan and convertible versions and b) Reducing the wall clock time of large scale problems by splitting the solution of different boundary conditions onto separate compute nodes. To demonstrate the use of MMO to solve problems with commonality constraints a body-in-white SUV model with multiple load cases is considered for the analysis. In one model, the SUV body is considered with the full roof structure and in the second model, the same SUV body is considered with a sunroof. The top of each vehicle is designed independently but the floor of both SUVs is design for commonality. The main example is solved using freeform optimization, however, other types of optimization such shape, sizing and topology are possible. The problem is solved using the GENESIS structural optimization software.