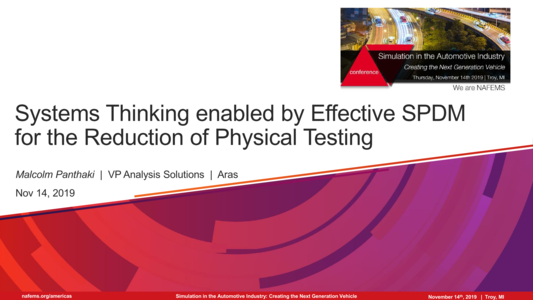
This presentation was made at the NAFEMS Americas "Creating the Next Generation Vehicle" held on the 14th of November in Troy.
The automotive engineering community is now confronting the largest technology transformation since its inception. This includes the electrification of powertrains for more efficient consumption and cleaner emissions, the reinvention of the battery with fast wireless charging capabilities and finally the advent of a fully autonomous vehicle. Compounding to these technology changes, the automotive companies design verification process is moving away from a major reliance on physical testing to almost a full virtual simulation product verification process.
The automotive engineering community is now confronting the largest technology transformation since its inception. This includes the electrification of powertrains for more efficient consumption and cleaner emissions, the reinvention of the battery with fast wireless charging capabilities and finally the advent of a fully autonomous vehicle. Compounding to these technology changes, the automotive companies design verification process is moving away from a major reliance on physical testing to almost a full virtual simulation product verification process.
Resource AbstractIt is 2019, and despite decades of software development, simulation continues to mostly exist within organizational silos that are geographically-distributed and isolated, not just from each other but from all other enterprise engineering processes and platforms. Also, simulation processes are limited to a small number of experts, is highly manual and error-prone, and hence, do not meet the global competition-driven need for rapid innovation and quick time-to-market. Hence, product teams continue to depend on physical testing to ensure product quality and to validate requirements.
As complexity increases, we see dramatic failures in the field, more and more, resulting in significant brand damage and warranty costs. The most technologically-advanced automotive manufacturers are beginning to realize that a pervasive culture of systems thinking is required for their siloed engineers to successfully manage the multidisciplinary nature of many of today’s products, while also considering the complex, interacting business, competitive, and operating environments in which they exist. While this has been common practice in the space satellite arena, automotive companies have only just begun to consider systems approaches. Furthermore, as product complexity and connectivity increase exponentially, intelligent simulation automation is even more essential, as manually-performed simulation, with its experts and data trapped in silos, becomes infeasible.
The primary emphasis of simulation point tools to accurately simulate more and more complex phenomena, while necessary, has had the unintended side-effect of encouraging siloed organizational structures. These silos isolate the simulation experts, their difficult-to-master point tools, and the related data, often resulting in incorrect inputs, simulation models that only the experts can use and outputs not available to the enterprise in a timely manner. This combination of expert-driven point tools and organizational silos thwarts the increasing need for multidisciplinary and multi-physics simulation automation and enterprise engineering data management – for simulation to be an effective enterprise product tool, something fundamental needs to change.
The authors believe that a requirements-driven, systems-centric unified data model within an open, vendor-neutral, extensible enterprise platform is a foundational building block. Such an approach supports multidisciplinary, multi-fidelity systems modelling and automation, extending the power of simulation to the broader product team. The product team, empowered to perform exponentially more simulations, can now depend less on physical testing. This data modeling approach must be complemented by more effective enterprise-wide Simulation Process and Data Management (SPDM), foundational to achieving closed-loop traceability with requirements, test results, design data and product field data. We believe this is an essential element of the digital thread architecture that is required to support a business and engineering culture that is powered by systems thinking.
The authors will present a reference architecture implementation that demonstrates the efficacy of the approach suggested in this paper. This reference architecture, based on an open, extensible, low-code product development platform, will bring together key elements of systems engineering (requirements and system architecture) with systems analysis and higher-fidelity simulation automation, powered by a unified data model. The system models form the connective tissue that enables the enterprise digital thread, with support for configuration management, variant management, and enterprise-wide data for timely decision-making.